SkLO: Material Matters
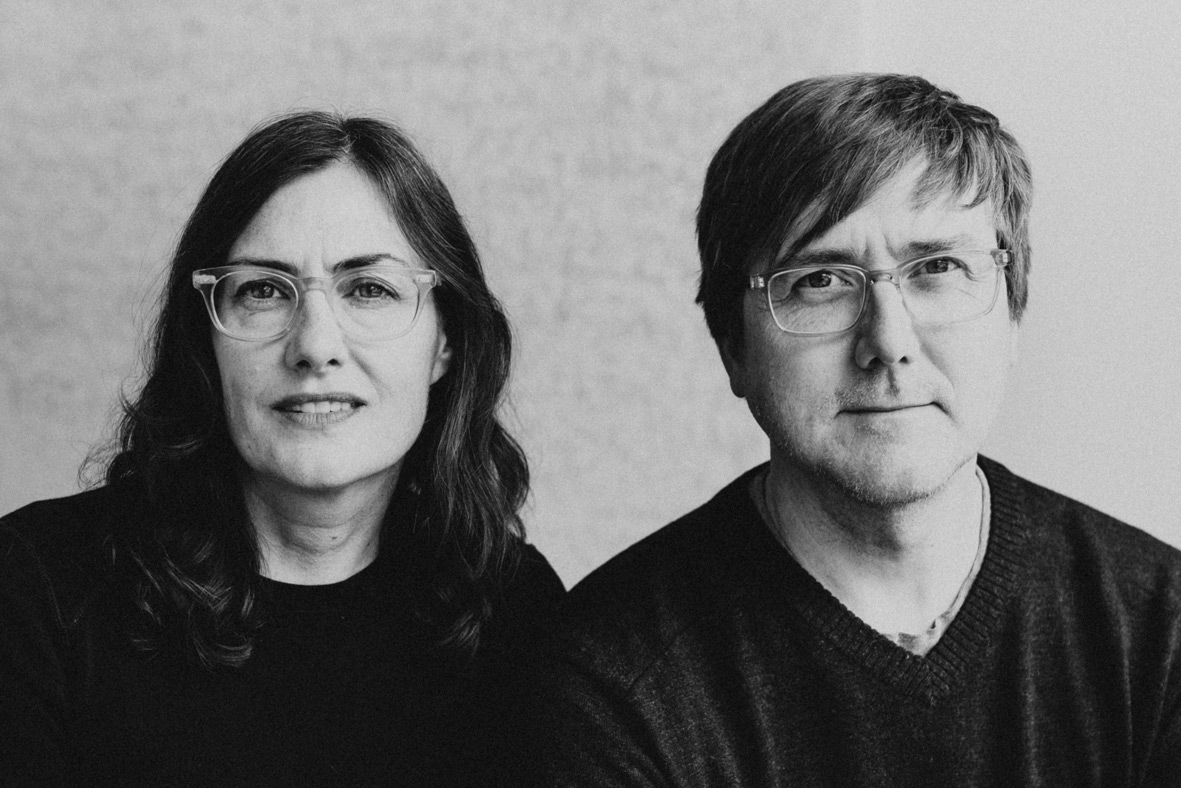
ICFF Brand Spotlight of SkLO
By Alia Akkam
In 2009, brothers Pavel and Petr Hanousek joined forces with Karen Gilbert and Paul Pavlak to found SkLO—that’s the Czech word for glass—a design and manufacturing business with headquarters in both Healdsburg, California, and Prague.
Serving as SkLO’s design partners, Gilbert and Pavlak, who are married, draw on their respective backgrounds—Gilbert a metalsmith and maker of jewelry, and Pavlak an architect with deep insight on proportion and scale and how they relate to the human body—to create the subtle yet sturdy hand-blown glass lighting and accessories collections LIT and OBJECT. Inspired by architecture, ceramics, and natural forms, Gilbert and Pavlak honor the Czech glassblowing heritage in a contemporary manner, melding glass with the likes of brass plates and arms and fashioning sculptural diffusers.
Here, Pavlak discusses SkLO’s reverence for both historic craft and an open-minded design process that embraces wabi-sabi.
What led you to establish a company grounded in the age-old art of Czech glassblowing?
Pavel, our partner and the SkLO CEO, has many decades of experience working with the glassblowing tradition in his native Czech Republic. It was Karen’s background, from living in Seattle in the 1990s and attending Pilchuk Glass School, which made her aware of the importance of Czech glassblowing and recognize the unbelievable potential of Pavel’s access to it. At the same time, Karen is herself deeply invested, educated, and working in craft, and that understanding was really the thing that SkLO grew from.
How would you describe the core of SkLO’s work?
Our design philosophy is a modern one, where we are trying to express the materials and the process of making them. One of the pitfalls of traditional craft is a focus on technique taking over at the expense of the final result. We are always trying to refine, to simplify, to allow the way the glass is blown to drive the design and the form. We do not want our glass to look ‘perfect.’ We introduce moments into the process of making that are slightly uncontrollable. Small elements of imperfection indicate that this is hand-made work. This is of supreme importance to us. One critical part of our design philosophy is that, in the end, it has to be beautiful. Good design, expert craftsmanship, yes, but we want our work to be beautiful to live with.
What is your approach to creation?
Glassblowing is an old way of making things, and it is a process filled with movement, subtlety, and expression of the individual makers. There is a lot of room in there. For us, it is important to bring our ideas to the glass, but also to be present and open to seeing what the glass has to show us. It is a process that demands understanding and rewards experimentation. Before the pandemic, we would travel regularly from California to our operation in the Czech Republic to visit the hot shops and oversee development of new work. We allow ourselves to make mistakes. Sometimes we just make what we call ‘parts.’ They might not have any clear use, but we will play around with them over time and that is when a direction shows itself, and we then pursue it to see if a final product is the result.
At ICFF, you planned to introduce a number of products that you then launched independently. Tell us about those.
We are tremendously excited about all of our work for the first half of 2020. Our new designs include the TWIN 2.0, a version of TWIN, which works as both a wall sconce and a ceiling flush-mount light; the VEER chandelier, a suspended light inspired by our VEER table/floor light; the DEW sconce, a version of our DEW pendant suitable for wall mounting; and the STEM 3X pendant and STEM 3X sconce/ceiling, fantastic new additions to our STEM collection.
Did the pandemic alter your point of view as designers?
The pandemic is an astounding global tragedy, a terrible shared experience for the entire human race to undergo. It is never easy to be a small business, but we cannot say that the pandemic has changed our perspective as designers. Perhaps it is to our advantage that we are somewhat slow to develop product. The nature of what we do, and the fact that we do not cut any corners in the making of our work, can mean that it takes a long time from idea to final product, so we have a lot of new designs already underway and we have continued with minimal interruption. Work and continuity are familiar and normal things, and to some degree it is soothing in that way.
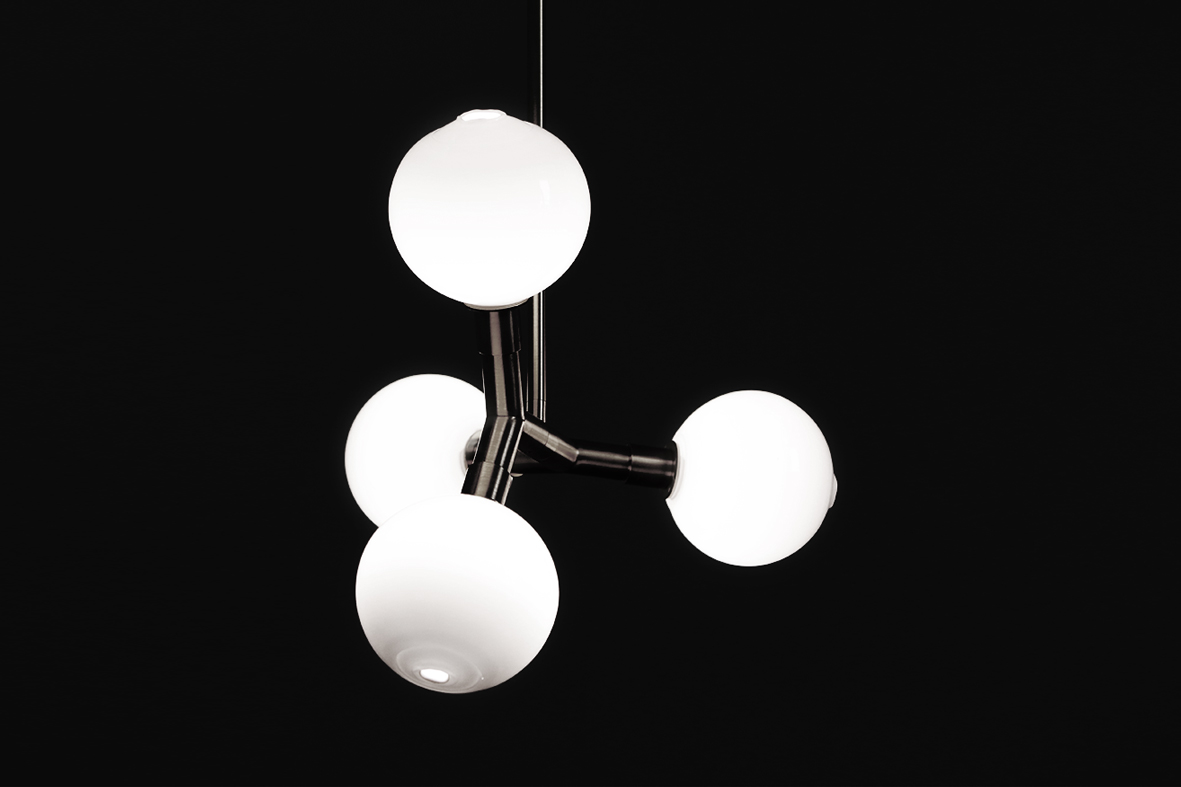
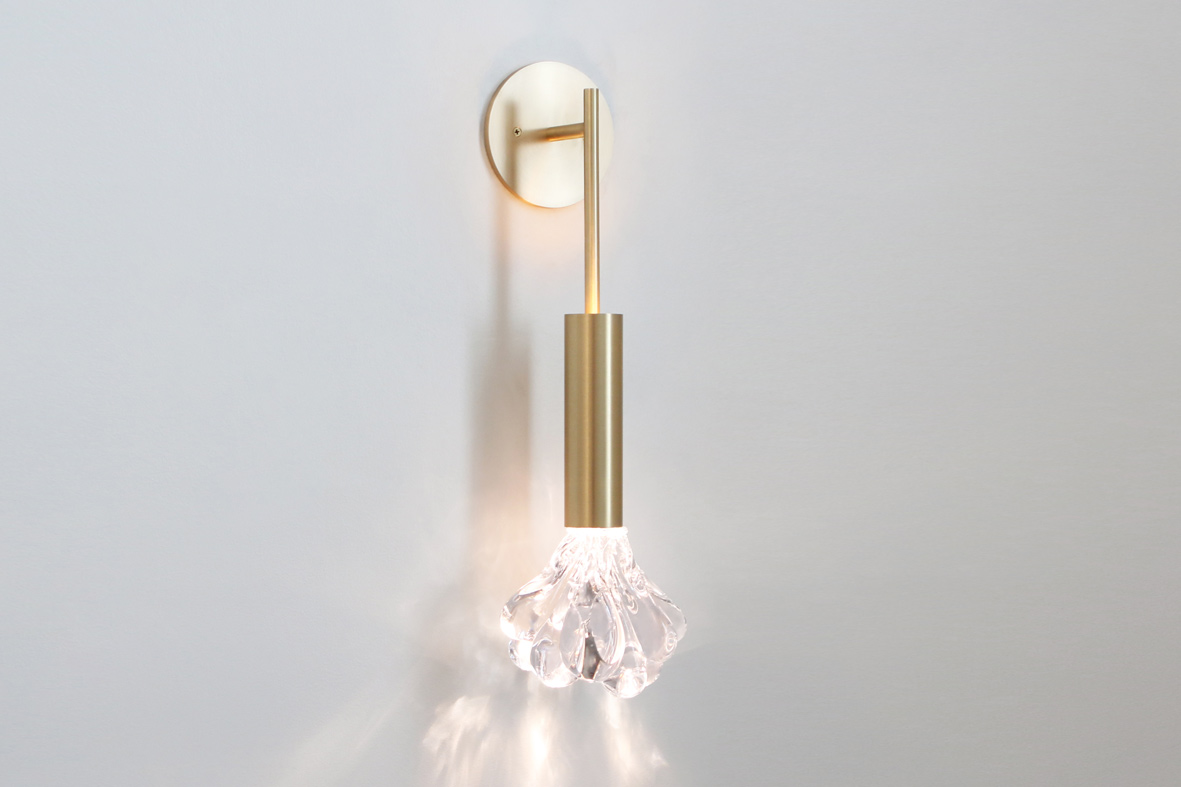
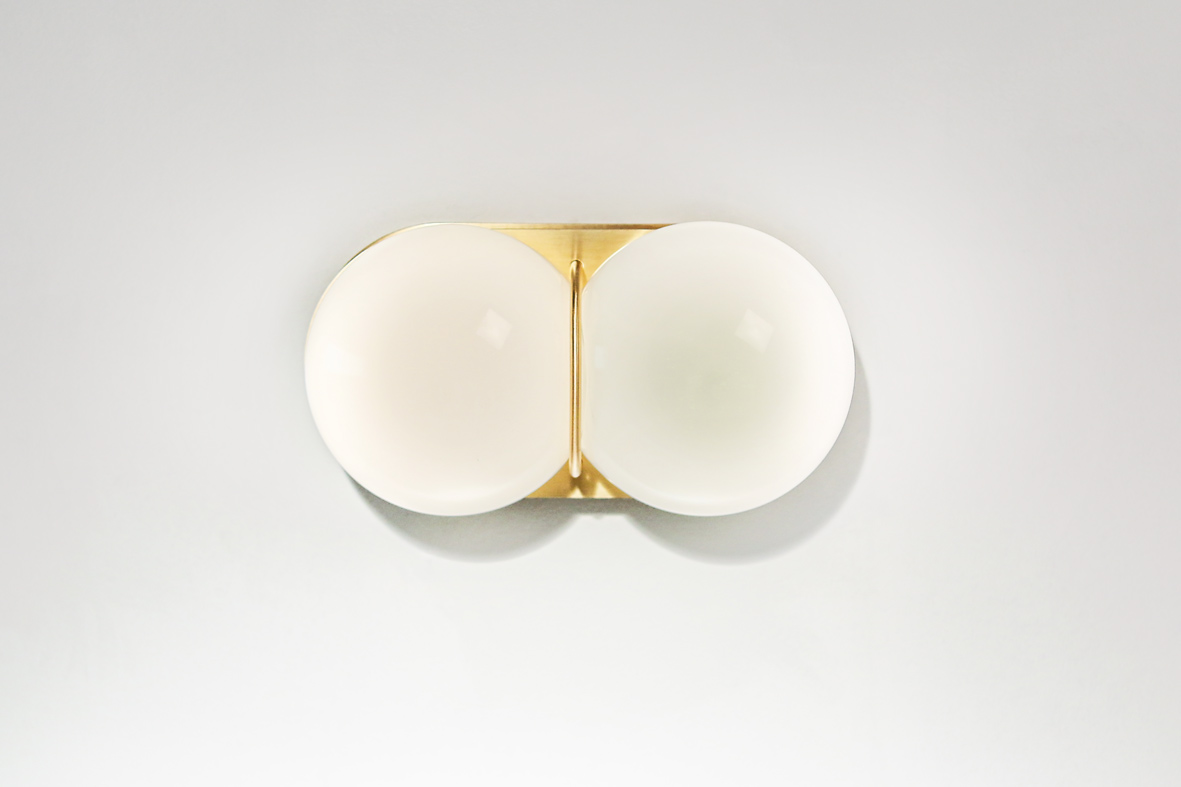
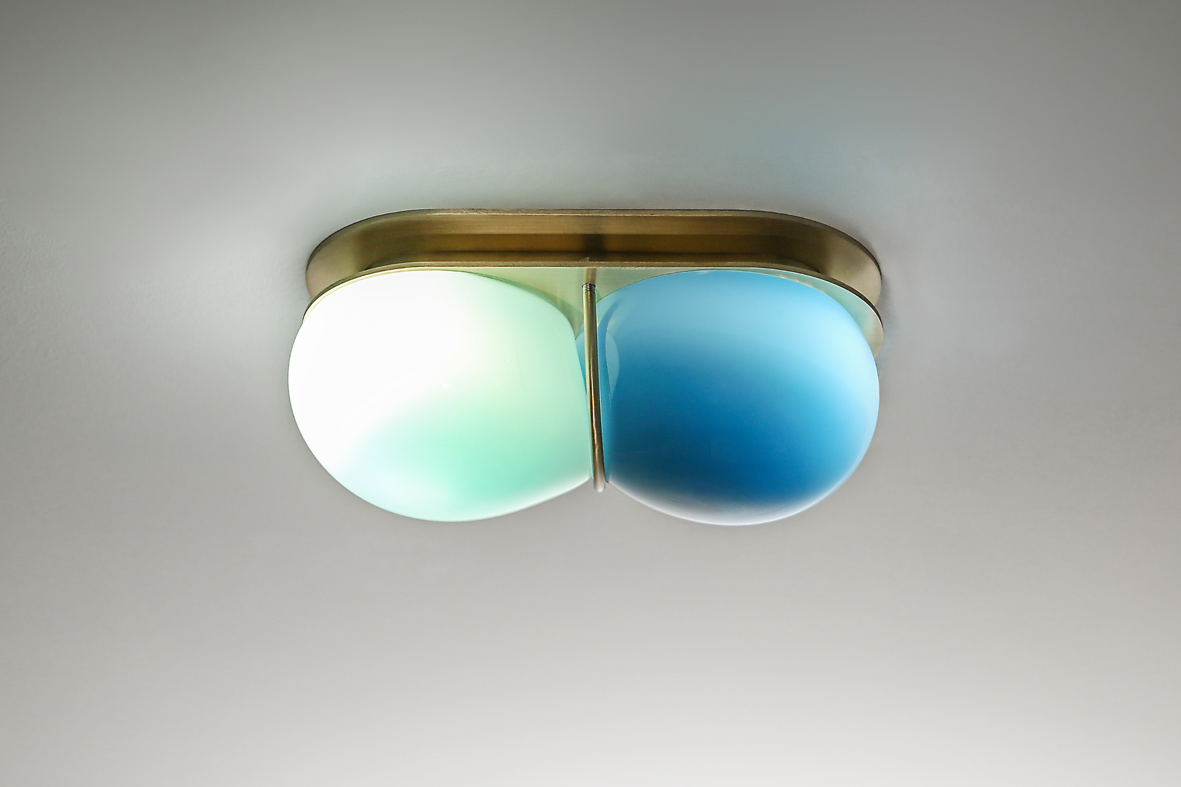
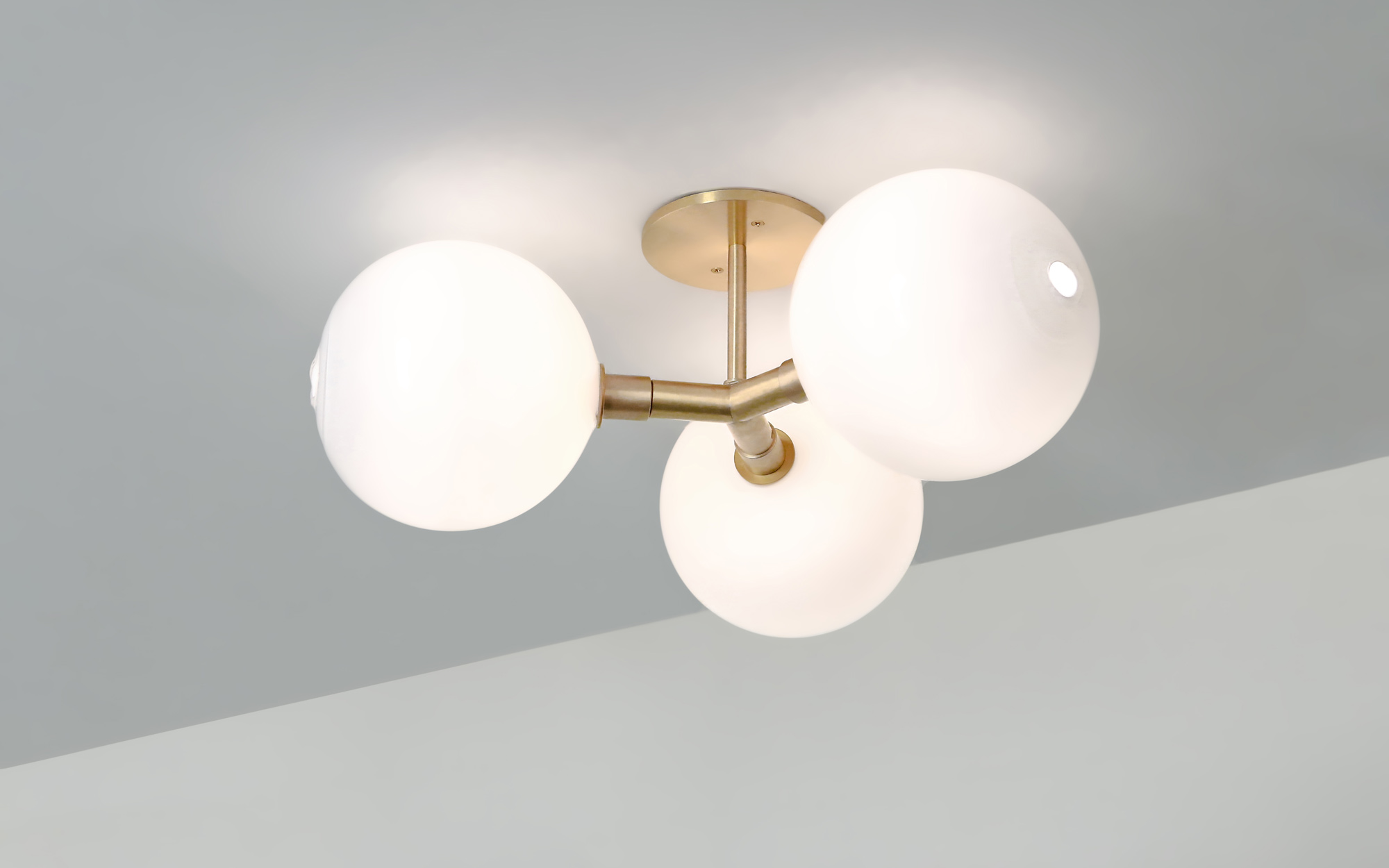
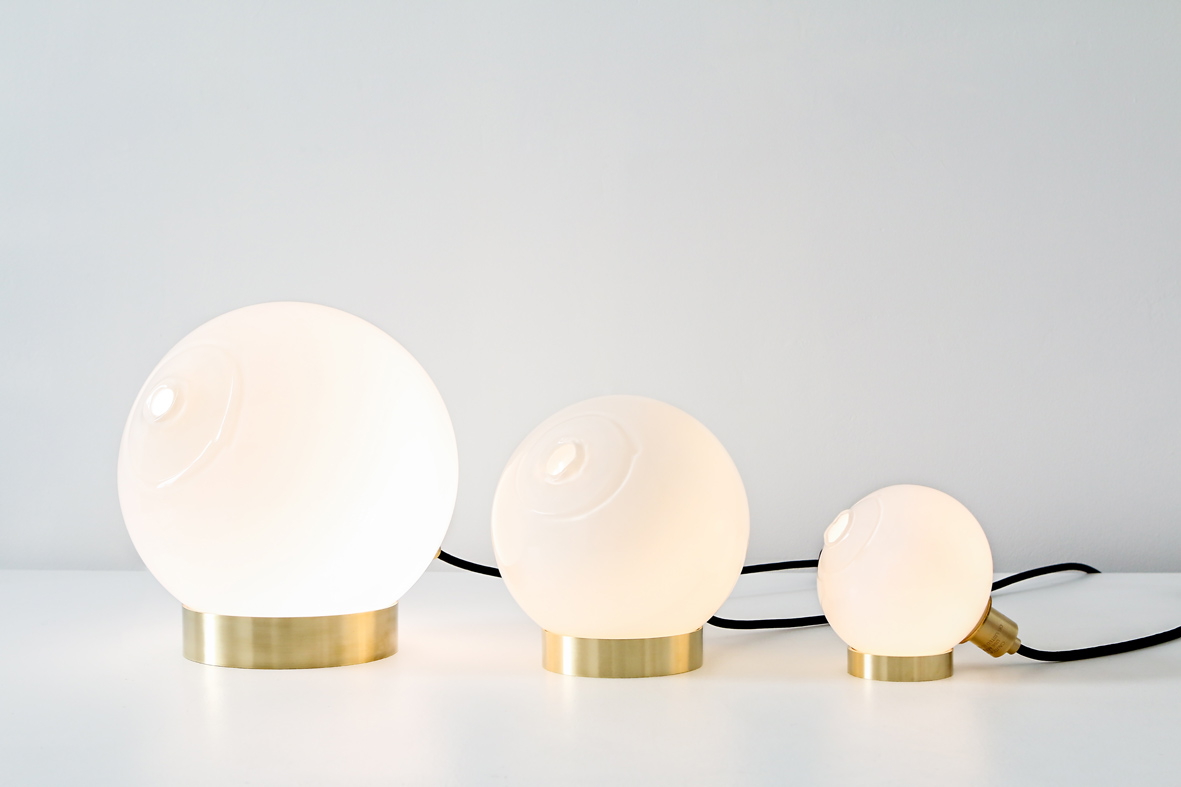